Blog
Boldt’s DBIA–WPR 2016 Award of Merit
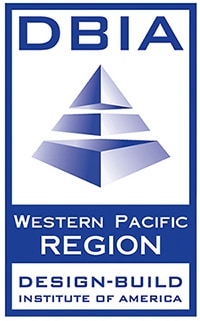
The 2016 Design–Build Institute of America Western Pacific Region (DBIA-WPR) Annual Design–Build Awards Banquet was held on May 26th, 2016 at the Newport Beach Marriott. This special event celebrated the winning projects and exemplary design-build teams of the region.
Boldt’s UC Davis Olson Hall seismic upgrades project was awarded the DBIA-WPR 2016 Award of Merit. This project was recognized not because it was a photogenic or glamourous project, but because of the hard work and dedication it took to overcome significant challenges and still be on budget and ahead of schedule.
The scope of the project included providing design and construction services for structural seismic upgrades to an existing building (Olson Hall) on the University of California Davis campus. The seismic upgrade work took place on three (3) floors (1st, 2nd, and roof) and encompassed approximately 60,000 sq. ft. Work that was supportive to the seismic upgrades included abatement of hazardous materials, concrete infill work and miscellaneous architectural improvements.
Project Goals
A major objective for the University was to complete all of the abatement and structural seismic upgrades inside the building during a time when it was least disruptive to students. Olson Hall is a well occupied building where classes are held daily. With the exception of school semester breaks, the owner required that the facility be turned over for use every Monday through Friday by 7 in the morning.
Recognizing the complexity of the work being undertaken and the risk of unforeseen conditions, the University ultimately decided to use design/build and issued the engineering documents set as “bridging documents” during the proposal phase in order to get design/build contractors on an apples-to-apples basis before awarding a contract. Once Boldt was awarded the project on best value, the University was open to suggestions and “out of the box” thinking in order to achieve their objective.
Challenges and Constraints
The first challenge was the very short design phase of ten days for design development and eighteen days for construction drawings. This did not leave much time for site reconnaissance, value engineering and design enhancements. A major schedule challenge was that the construction needed to fit between the winter semester break from December 22nd to January 4th and Spring Break from March 23rd to March 27th). This essentially meant that a five month project needed to fit within three working weeks. Another major challenge was with the hazardous abatement. Although a hazardous material survey was performed, there was the ongoing potential for delay associated with the discovery and remediation of unforeseen and unanticipated hazardous materials.
Solutions – Design Excellence
One of the design innovation examples would be for the reroute of the initial plan that included the infill of eight existing windows with concrete to create better structural support for the building. The structural engineer determined that by adding exterior concrete wing walls at the corners of the clerestory instead of filling the windows would accomplish the same structural improvements needed. This method reduced the number of concrete infill panels, which increases the amount of natural light through the building.
Another design element that was improved upon was the seismic upgrade material itself. The initial plan indicated that the first and second floors of the building were to receive fiber reinforced polymer (FRP) strips, the roof was to receive 18-inch wide steel plates and a support column in the basement required retrofitting with steel plating. Due to lack of space, existing plumbing and electrical conduits and devices would need to be relocated in order to complete these tasks. Instead, the team selected and approved use of an alternate FRP product that was higher in strength with fewer layers. Because of its capabilities, we were also able to use this product in lieu of the steel plates on the roof and basement column. The material not only met seismic design requirements, but was more quickly and easily installed in the field. This resulted in cost and schedule savings.
A third design improvement involved constructability. The initial plan included a considerable amount of relocation of existing mechanical, electrical and plumbing utilities. It also included demolition work that involved removing cross-corridor doors, fire rated doors and acoustical wall panels. These elements added complexity in design and represented a significant amount of the initial schedule. Boldt wanted the design to incorporate Lean constructability practices that would reduce the amount of demo and relocation work and make the seismic upgrade work easier and quicker to install in the field. With collaboration between the architect, structural engineer and trade partners, along with some creative thinking, the team significantly reduced the amount of demolition and relocation of existing utilities, walls and architectural items. For utilities that still required relocation, our mechanical trade partner offered constructability suggestions during the design phase that made the relocation more efficient in the field.
The owner could not have been more pleased with the result of Boldt and the rest of the project team’s collaboration. Teaming with trade partners ahead of time, including series of design meetings and onsite reconnaissance missions with our engineers and trade partners enhanced the constructability of the final design. It is because the collaboration and the Integrated Lean Project Delivery® that the project was able to be under budget and ahead of schedule.
About The Boldt Company
The Boldt Company (Boldt) is a leading professional construction services firm with customers across the United States and is a subsidiary of The Boldt Group. Founded in 1889, Boldt is a fourth-generation family and employee-owned firm headquartered in Appleton, Wisconsin. Boldt is recognized as a pioneer in Lean construction and in the industrialized construction space. Boldt operates 18 offices across the U.S. that serve customers in healthcare, power, industrial, education, automotive and commercial markets.