Blog
Quite a Ride – O.C. Boldt on Building a Company Legacy
On a sun-drenched summer afternoon, Oscar C. Boldt sits quietly inside Appleton’s Trout Museum of Art as installers carefully unpack a diverse collection of eclectic artwork.
As Pamela Williams-Lime runs through the last-minute arrangements for the exhibit’s opening, O.C., an avid supporter of the museum, asks the executive director a straightforward question:
“Pam, what do you need?”
Earnestly asked, the simplicity of the question belies its power. That simple query “What do you need?” may be the key question that has taken O.C. and the namesake company from a carpentry shop, started 125 years ago near Appleton’s downtown, to an nationally recognized builder of hospitals, schools, power plants and community icons.
When Boldt knows what a client needs, then it can build a building that helps the client accomplish its goals, whether that’s creating a safe environment to heal, a space conducive to learning or a more precise and efficient way to generate energy.
Knowing the answer to the question empowers Boldt to apply the knowledge and lessons learned over decades of projects, apply its award-winning Lean principles and create a building that delivers value to the client.
When Akron Children’s Hospital was searching for a firm to help guide a $200 million expansion of its campus, value became a factor that separated Boldt from other builders.
“Our Lean journey began in 2008, and with Boldt, we found a company that shared the same values,” says Grace Wakulchik, chief operating officer. “They approached things collaboratively and became a partner we trusted.”
It’s an approach that has resulted in a national portfolio of projects that will generate about $850 million for the company in 2014.
“Building can be a stressful experience,” says Bob DeKoch, president and chief operating officer for Boldt “If you treat the customer right, you can do great things. That’s part of everything we do.”
Humble origins
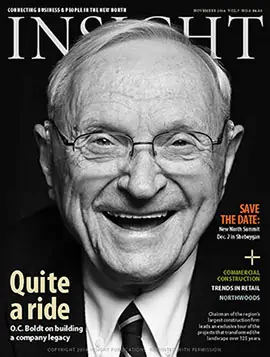
The origins of Boldt Company trace directly back four generations to Martin Boldt, who in 1889 announced the opening of his carpentry shop with an ad reading “honest and reliable contractor.”
That credo built a lasting foundation for Boldt. Oscar J. would take over the business and guide it through a period of expansion and incredible difficulty. His leadership during the 1920s through the 1940s would see the company expand into commercial and manufacturing construction, but also struggle through the Great Depression.
Despite the struggles, O.C., who would take over for his father following World War II, has fond memories of those days, even some of the projects that didn’t go so well. One of those included a very short stint by the family into the bakery business.
“My father originally built it for a baker, who basically went broke before he could get started,” O.C. says, pointing to a nondescript brown brick building across the street from the Fox Cities Performing Art Center. “It was the Depression. Another baker took over, but he didn’t last long, so my father took over the bakery to try and recover the building costs.”
“I can still smell the bread,” he says, as the car passes the building. O.C. accompanied this writer for Insight on a driving tour of landmark buildings the company has worked on during its 125 years.
Ultimately, the bakery failed. The building is still there, though, sitting on what would be the outer edges of the neighborhood where O.C., 90, grew up. A trip through the neighborhood evokes a range of memories and stories, from the house he grew up in — yes, it still stands — to an early location of the company to the ravine where he tore his new knickers while playing on a Sunday afternoon.
“Back then, getting something new was a treat,” he says. “Fortunately, my mother was able to sew them up.”
When it was finally his time to lead the family company, O.C. nearly took a pass.
As family legend tells it, O.C. Boldt struggled with the reputation many attached to working in the construction industry. As a whole, the industry was not always considered a reputable business at the time his father was deciding his future, says Tom Boldt.
Even with the values established by his father and grandfather, O.C. agonized over the decision.
“Our industry was not always known for its honesty,” says Tom Boldt, the current CEO and fourth-generation to lead the firm. “My father was really challenged by this. Could he do it his way and be successful?”
Fortuitously for Boldt, Appleton and thousands of clients across the continent, O.C. chose the family business and in four decades of day-to-day leadership, grew it from a handful of employees working on local projects to a national leader in construction services, with more than 2,000 employees and 14 offices in North America.
“At one time, we might have had fewer than seven employees,” says O.C. “I was the estimator, the auditor and just about everything else. I got pretty good at it.”
One of the other things he got pretty good at was building things for the paper industry. As that industry grew in the region, so did Boldt.
Boldt has applied the lessons learned from that experience to a wide array of construction markets, though it has become particularly well known in the education, energy and health care markets.
“Hydro work is pretty specialized, and we are fortunate to have them so near,” says Jeff Feldt, general manager of Kaukauna Utilities, which this past year completed a $38 million project to rebuild the intake canal and replace its Badger hydroelectric generating station.
“The resources they have on hand, the skilled craftsmen they can access and their management just stood out,” Feldt says. “We are getting a better performance than we expected.”
Industry innovators
Inside the conference room of the construction trailers at St. Elizabeth Hospital in Appleton, it looks like someone had a temper-tantrum with different color pads of Post-it notes. The multi-colored squares dotting the whiteboards around the room look a bit like an enlarged and pixelated image from a 1980s vintage video game.
Upon closer inspection, it all snaps into perspective.
The colored squares align with contractors and jobs and they are assembled, by date, on the whiteboards. Each day, the projects and dates are reviewed and squares adjusted to maximize coordination among various contractors on the job.
It may be low-tech, but the daily coordination process can reduce conflicts and avoid having one crew undo the work of another in order to get their part of the project done.
The whiteboards and daily site meetings are one part of the much broader Integrated Lean Project Delivery process created by Boldt executives in the late 1990s and used on every project they undertake. One of the charter members of the Lean Construction Institute, Boldt created its own process to deliver those principles, drawing on the lessons of 125 years of projects.
That process starts before the first shovelful of dirt is moved.
“The process had been around in manufacturing for some time, it just needed to be adapted to construction and project management,” DeKoch says. “We try to learn from every project, then apply that knowledge to the next project.”
The Integrated Lean Project Delivery®, commitment to sustainability and Boldt’s experience in health care construction were among the many reasons the company was tapped for this latest project at St. Elizabeth Hospital. The project, including a new 90-bed patient tower, is expected to be completed in early 2015.
For Gary Kusnierz, Affinity Health’s vice president for performance excellence, the commitment of the front-line employees was also a critical element of selecting Boldtfor the project.
“A lot of them have been working on projects here for more than a decade,” Kusnierz says. “They have almost become part of the staff. They consider it their hospital and they want to make it right for the community.”
That commitment fuels the desire to make sure the end product is the best it can be. Supervisors and contractors are empowered to draw on their experiences to suggest improvement. For example, the specs may call for the use of a certain product, but a contractor knows of a better solution.
Boldt Co. managers will use that information in discussions with the client to ensure the completed project meets expectations.
“There was a project we did for St. Olaf (College in Minnesota) that called for a window our subcontractors knew was a problem,” O.C. says. “We wound up saving $1 million from the original recommendation.”
As the company has further refined its processes, it has had one peculiar result: Boldt doesn’t often participate in the “competitive bidding” process. While the process is set up to provide the lowest cost to the client, it often does not allow the flexibility for Boldt to use its experience and processes to deliver maximum value in the finished product.
Instead, Boldt works on building relationships that lead to additional work.
“They have quite a body of work here on campus,” says Pete Sandberg, assistant vice president for facilities at St. Olaf College. “They are such an upstanding company, and it goes all the way from the guys at the top to the guys on the site.”
Boldt has been working on the St. Olaf campus since a library expansion in the 1990s. When new projects arise, the school often turns to Boldt. Sandberg says the company’s approach and shared values have played an integral role in keeping that relationship going.
“A lot of companies will ask ‘Why?’ They choose to ask ‘Why not?’” Sandberg says. “They are all about delivering value and are not threatened by listening to the ideas of others.”
Memory lane
A large portion of the lessons and knowledge Boldt brings to each project were learned in Appleton during the company’s formative years. A tour of Boldt-built projects is like a trip down an extended memory lane — there seems to be a building on every street where Boldt played a role in its construction or renovation in some way.
O.C. loves to show them off.
In preparation for this afternoon tour of the city, his short list of sites to visit fills both sides of a notecard, just a few ideas he jotted down. And each one has a story, some as important milestones for the company, and some much more of a personal highlight.
Sometimes the two come together, like they do for the Lawrence University campus.
There are the buildings, for sure, including one that makes O.C.’s personal top three list: the Warch Campus Center. The $35 million, 107,000-square-foot building is the largest in the school’s history, has won multiple awards and was the first education building in Wisconsin to achieve LEED Gold certification.
“We were shooting for silver, but with their help we were able to get gold,” says Lynn Hagee, director of special projects at Lawrence. “They did a great job of keeping us informed what was going on with the building all the time.”
The Warch project had its challenges. The university wanted student input included, and Boldt made sure their opinions were accounted for, going as far as building a replica wall with different stone patterns and holding a pizza party so students could decide on the look they liked, she says.
As construction was about to begin, it was learned the building next to where the Warch Center is located was slipping down the hill toward the Fox River. Boldt was able to develop and install a solution before the new construction aggravated the problem.
The Warch Center is also very near the building in which his wife Pat lived as a student at Lawrence when the two began dating. The couple celebrated their 65th wedding anniversary this year.
O.C.’s zeal and passion for work nearly bubble over when showing off what’s been done on the Lawrence campus. A gate restricting vehicle access to the interior campus serves as a testament to the value of experience when confronted by obstacles.
“I wonder if my code still works,” O.C. says, stepping out of the car to punch numbers in the keypad. Moments later, he waves the car through and rejoins the tour. “OK. Now I’m just showing off.”
Game changer
At the opposite end of downtown Appleton stands one of the other buildings on O.C.’s top three list and perhaps it is truly his favorite: the Fox Cities Performing Arts Center.
Certainly, it has delivered value. The PAC has changed the very nature of downtown Appleton, bringing visitors and spending from all over the region and fostering a revitalization of the other businesses in the vicinity. It is estimated the PAC generates more than $17 million a year in economic activity for the region.
Not everyone was convinced the project, seeded by an $8 million gift from Aid Association for Lutherans as it was merging into what is now Thrivent, would succeed.
“It was high risk,” O.C. says. “We worked really hard to keep it from failing, but we were pretty confident we would be successful.”
“We’d be a very different community without Boldt,” says Walter S. Rugland, the former COO of AAL who worked closely with Boldt to build the PAC. “They have built great partnerships with many people in this community.”
It’s not just the buildings, Rugland says, but the philanthropic efforts, many of which are performed quietly and without fanfare because the company and its leadership believe it is the right thing to do.
The PAC is also home to one of the great local legends involving O.C. and his passion for the project.
If you look closely on the building’s College Avenue exterior, just to the side of the main entrance, you will see a set of handprints. Those are O.C.’s hands. As the story goes, he was making a late-night visit to the site during construction and stepped back to get a better view, pushing his hands into fresh plaster. That was in the interior of the building. Before it was repaired, a cast was made and later installed on the exterior of the building.
Road ahead
While O.C. has remained an active force for Boldt — he still reads weekly reports updating ongoing projects — the company’s day-to-day leadership is provided by DeKoch, COO since 1990 and president since 2002 and Tom Boldt, CEO since 1990. O.C. remains as chairman.
They are committed to building on the reputation Boldt has built.
“It’s a source of pride to be a part of that,” DeKoch says. “He has curated a responsibility to helping our customers to get the most they can for the money they are spending and enjoy the experience.”
While Tom Boldt comes from a long line of builders, he did not set out to become one. A self-professed “liberal arts creative guy,” he came to the company later in life, a champion of sustainable and Lean building processes.
“We are working with companies that measure success and value in decades, not just quarterly results,” Tom Boldt says. “Those are values important to them and important to us.” The two have kept Boldt ahead of the curve.
Boldt recently signed an agreement with Akron General Health System to build wellness centers across the country. Boldt is also involved in hospital and health care projects throughout California.
While the Great Recession resulted in some belt tightening and layoffs, Boldt’s geographical and industry diversity allowed it to avoid the massive contractions that hit so many other companies. When things were slow in the Midwest, work was picking up on the coasts. As large commercial projects slowed, the energy sector boomed.
While well known for its involvement in big projects, Boldt has never undervalued the importance of small projects.
They may not get the headlines, but they are important to clients and play an important part in the company’s portfolio. DeKoch says the company will this year work on nearly $90 million in projects that are valued at under $500,000 each.
All the while, the company has maintained its leadership in LEED and green construction techniques and is making extensive use of technology with building information modeling techniques that create a 3D model of a building for a virtual walkthrough that can identify potential problems before a job starts.
Again, it’s part of the company’s mantra to deliver the best building possible for a client.
“Did we create an environment that people wanted?” Tom Boldt says of their evaluation of each project. “Knowledge and experience is important. We need to use it to make sure we do it better each time.”
About The Boldt Company
The Boldt Company (Boldt) is a leading professional construction services firm with customers across the United States and is a subsidiary of The Boldt Group. Founded in 1889, Boldt is a fourth-generation family and employee-owned firm headquartered in Appleton, Wisconsin. Boldt is recognized as a pioneer in Lean construction and in the industrialized construction space. Boldt operates 18 offices across the U.S. that serve customers in healthcare, power, industrial, education, automotive and commercial markets.