Blog
The Impact of Industrialized Construction
The U.S. construction market was valued at $2.1 trillion in 2022 and is expected to achieve an annual average growth rate (AAGR) of more than 4% during 2024-20271. To be part of this projected growth, construction companies are looking beyond traditional construction and achieving success using Industrialized Construction (IC) methods. Consequently, prefabrication and modular construction—two components of industrialized construction will see overall growth as well.
Challenging the Norm
Industrialized construction addresses some of the most complex issues of present-day building including extended timelines, scaling constraints, and volatility created by variable projects and conditions. Recent advances in technology, construction, and delivery methods have led to a renewed interest in IC as a more efficient, cost-effective and sustainable approach to building that can be applied to almost all market sectors from healthcare, to power and energy, to food and beverage.
Around the industry, “prefabrication” and “modular construction” are used to describe the type of work being done under the industrialized construction banner. Simplified, IC brings a manufacturing mindset to construction components and subassemblies. The Boldt Company’s Director of Design Integration Jenny Han asserts, “a prefab/modular solution involves a highly controlled, factory-based approach to manufacturing building components and onsite assemblies. The benefits are hard to ignore.”
In the early stages of industrialized construction, Boldt identified IC as an opportunity to improve efficiency and solve some of today’s major construction issues. It allows for optimizing fabrication and implementing numerous strategies to streamline the production process. The benefits: improvements in safety, productivity, quality, speed and performance, while maximizing resources like materials and labor.
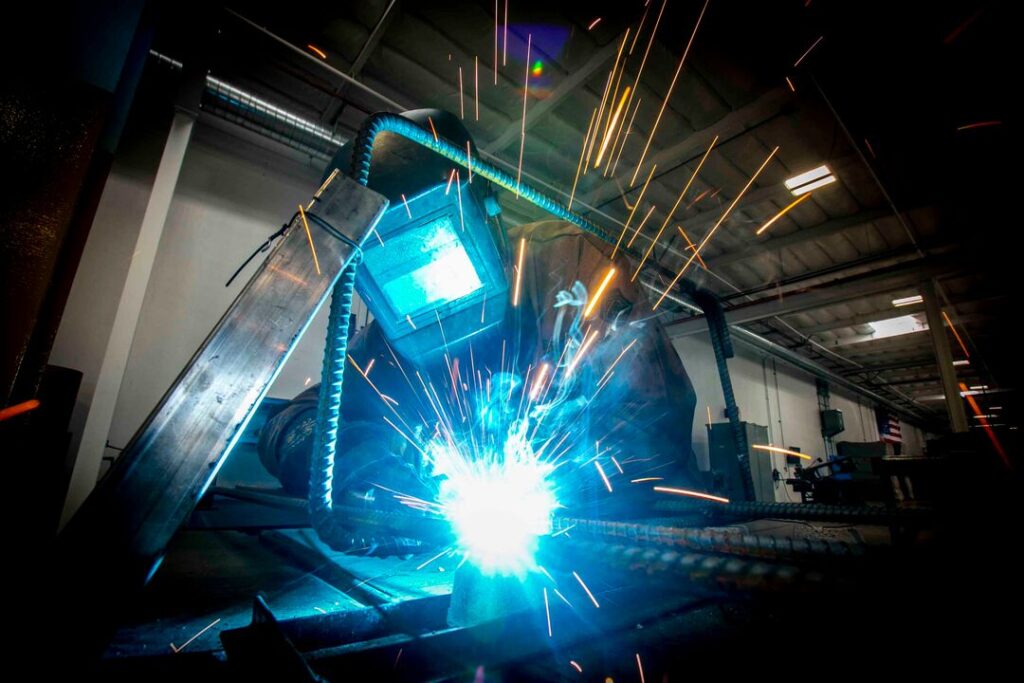
Key Advantages
- Speed to market: Fast tracking the rate of construction is accomplished by leveraging standardization, prefabrication, improved project management and faster assembly timelines resulting in shorter construction times and quicker project delivery.
- Safety: Working in a controlled factory environment eliminates exposure to harsh weather elements and provides greater control over potential safety hazards.
- Standardization: Standardizing building components and materials can help reduce the time and costs associated with design and production, making the fabrication process more efficient.
- Precision: Building components can be manufactured off-site to a much higher level of precision, resulting in greater consistency and quality in the finished product.
- Lean manufacturing/construction: Lean manufacturing principles are intrinsic to the fabrication process to eliminate waste, reduce labor costs and improve quality.
- Quality control: Implementing a robust quality control system ensures that the finished products meet the required standards and specifications, reducing the need for rework and delays.
- Material selection: Choosing materials that are readily available, cost-effective, and easy to work with improves the overall efficiency of the fabrication process by using standardized building components that are optimized for efficient production and assembly. This reduces the amount of material waste generated during construction and minimizes the carbon footprint associated with transporting materials to the construction site.
- Skilled labor management: The construction industry is facing a shortage of skilled labor, which is driving up costs and causing delays in project timelines. IC offers a solution that reduces the reliance on on-site labor, allowing for faster and more efficient construction.
- Supply chain optimization: Managing the supply chain effectively can help reduce lead times, lower costs and ensure timely delivery of materials and components.
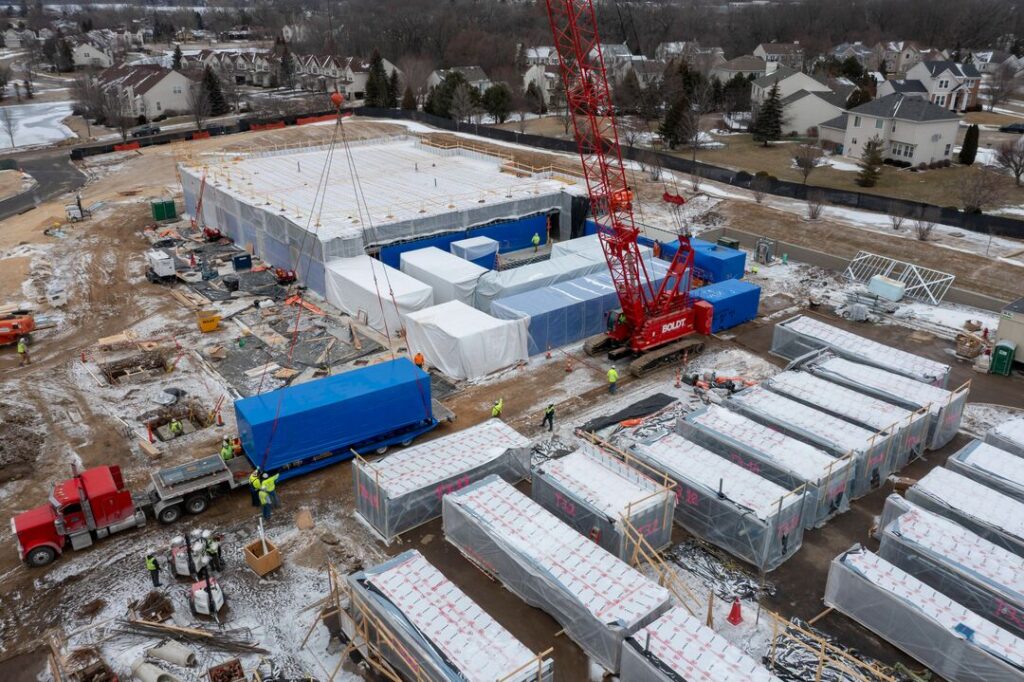
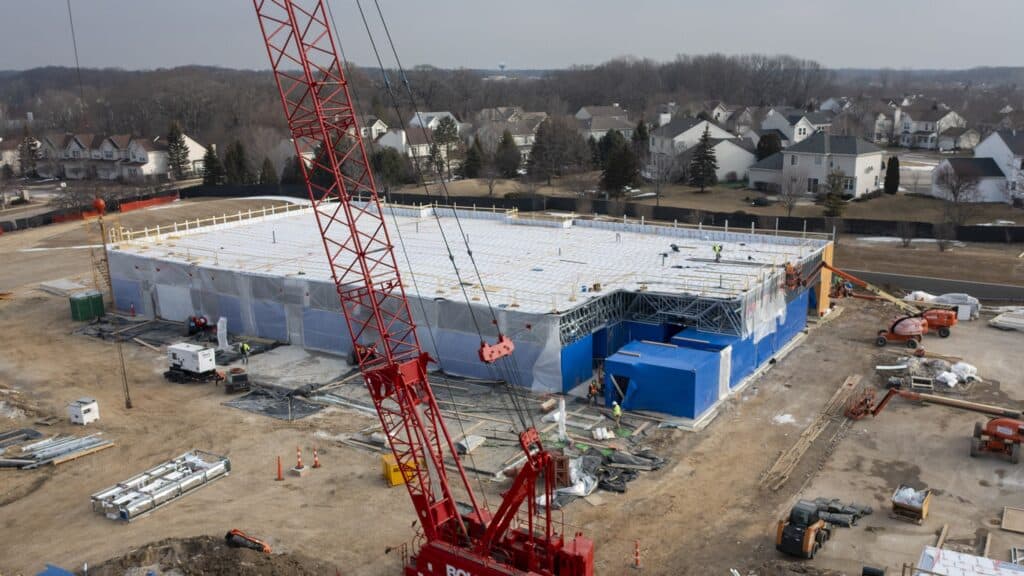
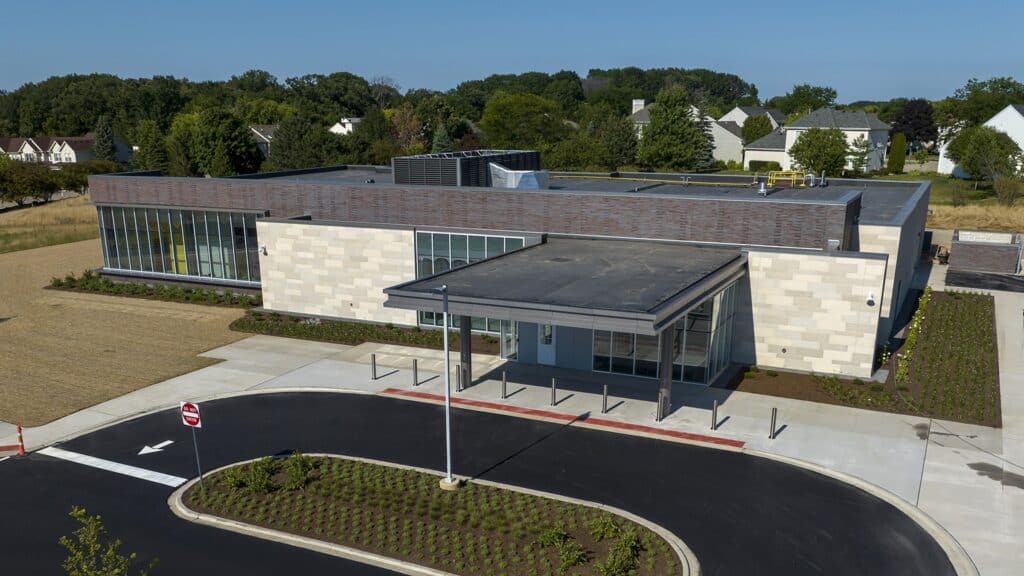
If You Want to Build Things Differently, You Need to See Things Differently!
Optimizing the fabrication process in IC involves a holistic approach that considers all aspects of the production process, from initial conceptual design and material selection to production and delivery, to setting and connections. It involves moving from a “project” mentality to a “product” approach. By implementing these strategies in the manufacturing process, Boldt can increase efficiency, reduce costs and improve the overall quality of the finished product.
There’s a single source of truth, offers Han. “Having dozens of consultants, trade partners, and production crews involved during various stages of the design and manufacturing processes, along with limited MEP space and the necessity for spot-on connections between modules requires a high level of collaboration and transparency. IC helps us achieve our customer’s goals of delivering construction projects faster, achieving a higher quality of product, and finding a safer way of delivering projects all within the pursuit of reducing capital costs.”
Over time, industrialized construction techniques have been refined and expanded to include a wide range of building types such as inpatient hospitals, ambulatory medical centers, commercial spaces, schools, and even entire neighborhoods. As the construction industry continues to evolve to meet current and future demands, it’s likely that modular construction and prefabrication will play an extensive role in challenging construction norms and shaping the future of building.
From prefabrication to modular construction solutions, owners are turning to Boldt. IC continues to be a proven approach for better project outcomes—from budget reliability to safety and faster speed to market.
Check out these recent Boldt prefabrication/modular projects that delivered game-changing results:
Aurora Medical Center—Grafton, WI
Industrialized construction provided an exceptional product, safer working conditions, and faster speed-to-market for Advocate Aurora Health’s recent expansion at Aurora Medical Center in Grafton. An ILPD culture maximized the team’s unique expertise and led to the first of its kind, fully integrated volumetric modular solution.
Advocate Medical Group Dreyer Health Clinic—
Naperville, IL
If you want to build differently, you have to see things differently. Where some saw an old grocery store, we saw a modern healthcare clinic. Prefabricated modular units were used to create exam rooms, support areas and office space for the renovation of this Advocate Aurora Health project in Naperville, Illinois.
Advocate Medical Group Outpatient Clinic—
Lake Villa, IL
Boldt’s first fully prefabricated/modular outpatient clinic. 90% of the facility was modularized and prefabricated off-site, reducing the overall schedule by two full months. A total of 29 modular room pods, 43 roof pods and 18 multi-trade racks were created and installed.
Marshfield Clinic Health System—Marshfield, WI
Marshfield Clinic Health System needed a way to connect its existing hospital with an east wing building, but building at ground level would have significantly disrupted daily operations. Instead, construction teams were tasked with building a “tunnel in the sky” to transport patients, linens, food, and supplies needed for everyday support. Trusses for the tunnel were prefabricated in an empty parking lot near the campus and moved to the site.
Resources:
1 Globaldata.com: https://www.globaldata.com/store/report/usa-construction-market-analysis/
Construction review online: https://constructionreviewonline.com/modular-and-prefabs/advantages-in-adopting-prefabrication-and-modular-building-construction-2/
BDCnetwork.com (2021): https://www.bdcnetwork.com/blog/epic-rise-industrialized-construction
About The Boldt Company
The Boldt Company (Boldt) is a leading professional construction services firm with customers across the United States and is a subsidiary of The Boldt Group. Founded in 1889, Boldt is a fourth-generation family and employee-owned firm headquartered in Appleton, Wisconsin. Boldt is recognized as a pioneer in Lean construction and in the industrialized construction space. Boldt operates 18 offices across the U.S. that serve customers in healthcare, power, industrial, education, automotive and commercial markets.